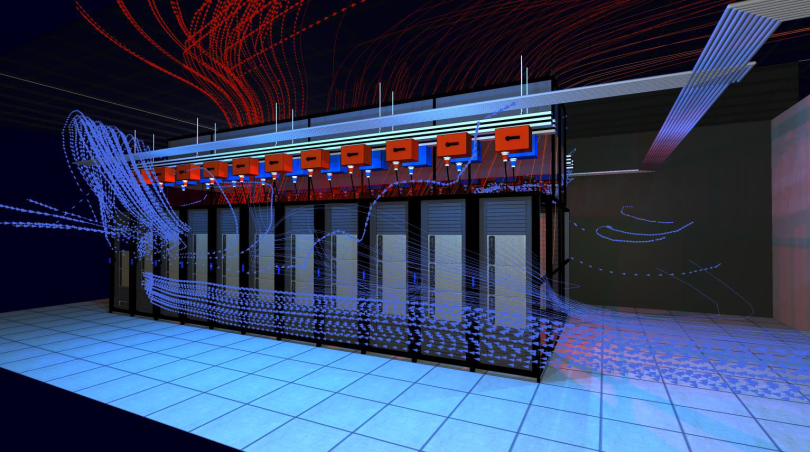
What a long way we’ve come! From the first Ford assembly line in the early 20th century to the digital-twin revolution, industry has undergone constant change. Today, these virtual replicas are providing an opportunity to design, test and optimise complex systems in real time, redefining standards of efficiency, sustainability and innovation. This revolution and shift in practices is opening up a huge range of possibilities in multiple sectors, from manufacturing to healthcare, digital infrastructures, construction and data centers.
Made possible by the interconnection between artificial intelligence (AI) and data centers, digital-twin technology is currently revolutionising industry. The idea is to model physical systems in virtual environments to improve their design, efficiency and sustainability. Whether in the field of data centers, healthcare, manufacturing or construction, the number of use cases is increasing in France and around the world – and the possibilities seem endless.
Digital twins originated in the aerospace industry in the 2000s, when NASA used them to simulate and monitor the operation of systems during space missions. This technology has since evolved to be applied to many different sectors thanks to the rise of AI and the Internet of Things (IoT).
A wide range of uses
In the field of healthcare, digital twins are offering many promising opportunities for preventive and personalised medicine. For example, they can be used to create digital models of the human body to simulate medical treatments before they are actually applied. These virtual replicas are also facilitating the training of healthcare professionals and accelerating clinical research by testing various response scenarios for complex pathologies such as comorbidities and rare diseases. European programs such as EDITH (European Virtual Human Twin) are bringing together researchers, clinicians and industry to roll out innovative solutions.
The manufacturing industry is also making extensive use of this technology to optimise production lines. Car manufacturers are using digital twins to virtually design and test their vehicles, thereby reducing prototyping costs and accelerating time-to-market. In factories, these models are providing a way to monitor machine performance in real time, identify bottlenecks and improve operational efficiency.
The construction sector is benefiting from digital twins as well, using them to model complex infrastructure projects to optimise their sustainability and environmental footprint. Town planners are turning to interactive models to simulate traffic flows, climate impacts and resource requirements. In the operational phase, they can facilitate the predictive maintenance of buildings and infrastructure, by detecting anomalies before they become critical.
Logistics and supply chains are also making the most of digital twins, which they can use to simulate and anticipate possible disruptions. Companies are adopting this technology to optimise transport flows, reduce operational costs and improve resilience in the face of crises, as demonstrated by the COVID-19 pandemic.
“This technology has come a long way since the 2000s to be applied to many sectors thanks to the rise of artificial intelligence and IoT.”
The data center sector is no stranger to this revolution, as this technology is helping to optimise the management of these infrastructures by simulating thermal and energy flows. The management of cooling systems – whether free cooling or direct liquid cooling – has become much more precise, for improved energy efficiency. In addition, real-time analyses are enabling maintenance requirements to be anticipated using predictive models, thereby reducing service interruptions and extending the lifespan of equipment.
A cross-disciplinary tool capable of improving innovation and sustainability in a wide range of sectors, this technology is considerably increasing their ability to predict, simulate and optimise physical processes. It is opening up major opportunities for companies seeking to combine operational performance and environmental responsibility. With the rapid growth of AI and IoT, applications of digital twins will continue to multiply, positioning this technology as a driver of change in the decades to come.
Data4 adopts digital-twin technology with Wattdesign
A pioneer in the introduction of digital twins tailored to the data center sector, the French company Wattdesign is preparing to deploy this technology for one of our customers hosted on the Marcoussis campus (Essonne).
What is a data center digital twin? A digital twin is a virtual 3D replica of a data center that can simulate its physical behaviour in any operating scenario. It provides a virtual representation of a data center’s ‘building blocks’, i.e. the power supply chain, the cooling system and the IT equipment of all major OEMs.
“The digital twin is a virtual 3D replica of a data center that can simulate its physical behavior in any operating scenario.”
As an “augmented” DCIM solution, digital twins provide very detailed feedback in real time. They also make it easier to predict and monitor how changes will impact a data center’s performance and IT production.
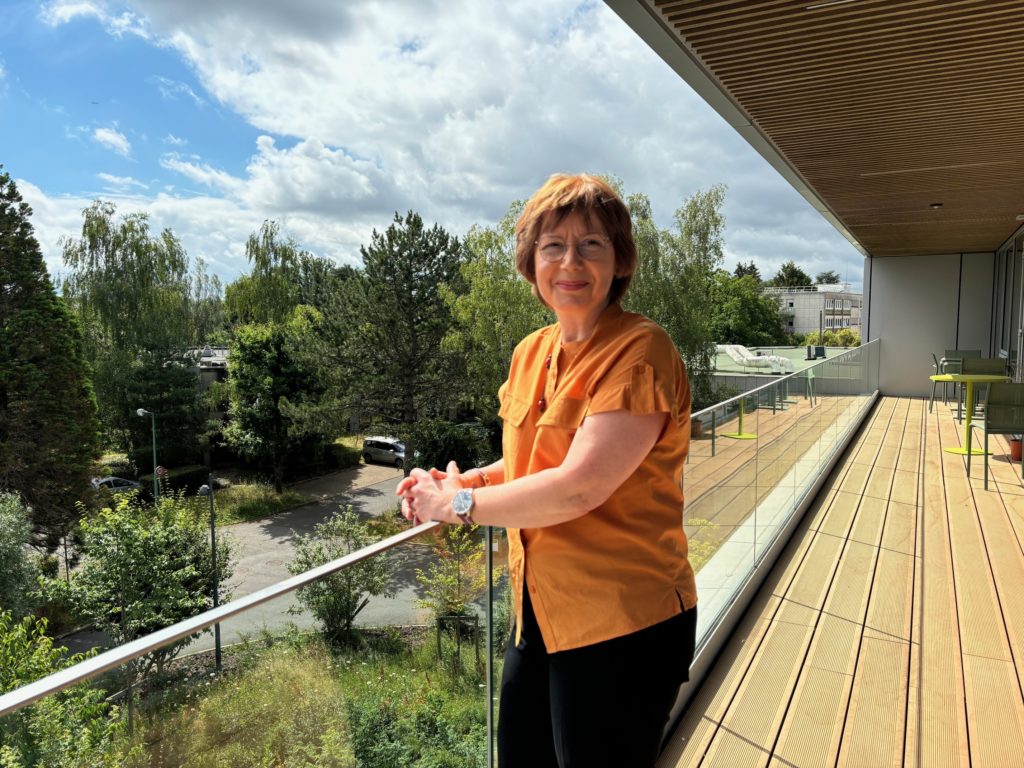
Sylvie Boudoux, director and founder of Wattdesign, explains: “This digital replica optimises data center asset management by modelling the entire electrical chain, guaranteeing redundancy and load balancing. By anticipating breakdowns and analysing their impact, it ensures continuity of service.
It is an essential tool for capacity planning, offering a forward-looking vision of how rooms will develop. It also enables cooling to be optimised via airflow simulation (CFD), thereby improving energy performance and reducing PUE. Moreover, by integrating real data, this technology helps to assess the carbon footprint of infrastructures (Scope 1, 2 and 3 emissions).
For Bank of America Merrill Lynch / CBRE, it has raised the supply air temperature by 5 degrees, generating $1.5 million in savings, i.e. 4,000 tonnes of CO₂ avoided within 24 months, with a 15% reduction in PUE and recovery of 350 kW of lost capacity, for total savings of $8.75 million and ROI within four months”.